Hydraulic System Failures in Lift Gates: Diagnosis and Fixes
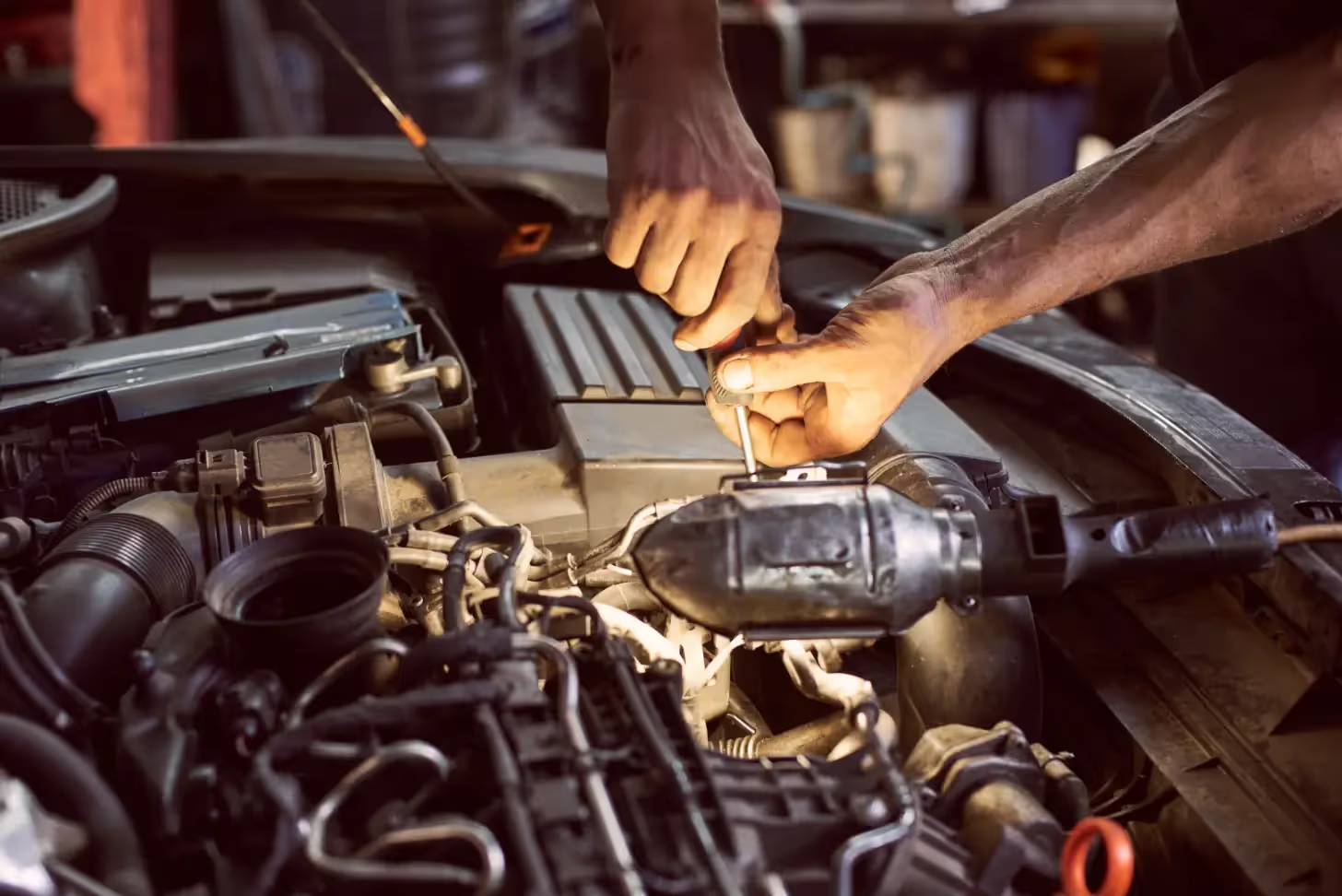
In the transportation and logistics sector, lift gates serve a pivotal role in streamlining operations. Whether you’re loading palletized goods at a warehouse or delivering merchandise in urban environments like Chicago, IL, a malfunctioning lift gate can be more than a mere inconvenience—it can lead to significant operational delays, safety concerns, and financial losses. Central to the operation of these gates is the hydraulic system, which relies on pressurized fluid mechanics to raise and lower heavy cargo efficiently. When this system fails, quick and accurate diagnosis, coupled with reliable repair solutions, becomes critical.
This article explores the complexities of hydraulic system failures in lift gates, providing a detailed examination of their causes, symptoms, and repair procedures.
The Inner Workings of a Hydraulic Lift Gate
To properly diagnose a problem, one must first understand the underlying mechanism. A combination of mechanical and electronic components powers a hydraulic lift gate. At the heart of the system lies the hydraulic pump, which pressurizes fluid stored in a reservoir and sends it through a series of hoses to actuator cylinders. These cylinders convert fluid pressure into linear motion, allowing the gate to rise or descend. An electronic control unit (ECU) or manual switch governs the operation, signalling the pump when to activate and regulate fluid flow.
Because these components must work in perfect harmony, even a minor malfunction in one part can cascade into a complete system failure.
Common Causes of Hydraulic System Failures
1. Hydraulic Fluid Leaks
The most common issue faced in truck lift gate systems is the leakage of hydraulic fluid. Whether due to a cracked hose, a damaged seal, or a loose fitting, fluid loss compromises pressure levels and impairs lift function.
Diagnosis and Repair: A visual inspection can usually confirm the presence of a leak—look for puddles beneath the lift gate or residue around hose fittings. Use UV dye or hydraulic leak detection spray to trace minor leaks. Replace damaged hoses, seals, or fittings promptly, and ensure fluid is topped off to the manufacturer's specifications.
2. Air Entrapment in Hydraulic Lines
Air in a hydraulic line acts as a compressible barrier, diminishing the system's ability to build and maintain pressure. The result is often a jerky lift operation, sluggish response, or outright failure.
Diagnosis and Repair: If the gate hesitates or moves unevenly, suspect air contamination. To correct this, bleed the system by cycling the gate through several complete movements, keeping the reservoir cap off and observing the fluid levels. Most modern systems include bleeder valves for efficient air removal.
3. Pump Motor Failure
The hydraulic pump motor plays a crucial role in generating the pressure necessary for operation. If the motor fails to engage or makes unusual noises, internal wear or electrical faults may be the cause.
Diagnosis and Repair: Use a voltmeter to test the power supply to the motor. If voltage is present but the motor remains inoperative, inspect for burnt windings, failed solenoids, or worn brushes. In some cases, the entire motor unit may need to be replaced.
4. Electrical System Malfunctions
Electrical issues can be as disruptive as mechanical failures. A defective control switch, frayed wiring, or blown fuse can interrupt communication between the operator and the hydraulic system, potentially causing issues.
Diagnosis and Repair: Begin by inspecting the switch and wiring harness for corrosion, moisture intrusion, or physical damage. Test circuits with a continuity tester and replace any components that fail. In older systems, upgrading to a weather-resistant switch may improve reliability.
5. Cylinder Damage
Hydraulic cylinders are subjected to extreme force and must remain perfectly sealed to function correctly. Bent rods, scored cylinder walls, or worn seals can lead to internal or external leaks, resulting in a complete loss of lift function.
Diagnosis and Repair: Inspect the cylinder for visible damage or fluid seepage. If seals are worn, rebuild kits may be used for repair. Severely damaged rods or cylinders, however, require complete replacement to ensure safety and performance.
Diagnostic Best Practices
Proper diagnosis is a structured process. Following a systematic checklist helps isolate issues and determine whether the failure is mechanical, electrical, or fluid-based.
Step 1: Conduct a Visual and Manual Inspection
Begin by inspecting the entire system for visible signs of wear, corrosion, or fluid leakage. Ensure all fittings and mounts are secure and that the lift gate platform is not obstructed or damaged.
Step 2: Evaluate System Response
Activate the gate and listen for motor activity. A functioning motor accompanied by no movement may suggest fluid blockage or cylinder failure, whereas silence often indicates an electrical issue.
Step 3: Check Hydraulic Fluid Condition and Level
Inspect the reservoir for sufficient fluid levels. Discoloured, milky, or gritty fluid may indicate contamination by water or debris, which reduces system efficiency and causes premature wear.
Step 4: Electrical Testing
Use a multimeter to test voltage at the control switch, solenoids, and motor terminals. Check for shorts or open circuits and ensure that grounding is intact.
Step 5: Pressure Testing
Using a hydraulic pressure gauge, verify that the system is generating the correct pressure in pounds per square inch (PSI). Low pressure may indicate a failing pump, a clogged filter, or an internal bypass.
Preventive Measures to Avoid System Failures
An ounce of prevention is worth a pound of cure—especially when it comes to complex hydraulic systems. Incorporating routine maintenance can dramatically extend the life of your lift gate and prevent unplanned downtime.
- Inspect hoses and fittings regularly for wear, cracks, or leaks.
- Change hydraulic fluid annually or according to the manufacturer’s schedule to avoid contamination buildup.
- Protect electrical connections with dielectric grease to prevent corrosion.
- Exercise the lift gate periodically, even during slow seasons, to keep seals lubricated and components functional.
- Clean the lift gate mechanism regularly, especially in urban environments like Chicago, where salt and debris can accumulate quickly.
When Professional Service Is Required
Despite the best diagnostic efforts, certain situations demand the expertise of a trained technician. This is especially true for:
- Major electrical faults
- Cracked or scored hydraulic cylinders
- Malfunctioning control modules
- System failures involving multiple components
Attempting complex repairs without the proper tools or knowledge may result in further damage or safety risks. If in doubt, always consult with a certified hydraulic technician who specializes in on-site truck service.
Conclusion
In the realm of commercial transport, efficiency and uptime are paramount. A malfunctioning hydraulic lift gate can cause severe logistical headaches. Fortunately, most failures originate from a small pool of predictable issues, such as leaks, electrical malfunctions, air contamination, or mechanical wear. By understanding the core components and maintaining vigilance with inspections and regular maintenance, operators can effectively mitigate downtime and ensure operational integrity.
For fleet managers and operators in Chicago, IL, staying ahead of hydraulic issues ensures that delivery schedules remain on track and vehicles remain compliant with safety standards. Whether you manage a single truck or an entire fleet, proactive maintenance and precise diagnostics are your best line of defence.